Mechanical Thermal Surveys
Thermal imaging surveys use the latest thermographic technology to screen for hot spots and areas of wear before equipment failure actually happens. This routine preemptive testing can save lots of money, from the cost of repair to the cost of equipment downtime.
The first signs of equipment failure can be a range of things, including physical mechanical failure, which is the worst-case scenario and can be deadly, if not extremely costly, in equipment plants or other settings.
What Does Mechanical Thermal Imaging identify?
The survey does not impact machine operation, it is a very non-invasive means of detecting issues. Below are just a few of the things that thermal imaging surveys can help with, in a mechanical setting.
Overheating of machines and equipment- The use of thermography in mechanical overheating can help prevent any major fires or breakdowns in machinery, which could cause harm to you and other people around.
Overheated Bearings- Thermal imaging helps to prevent strain that is put on the motor of any mechanical equipment, which could, in turn, cause your equipment to fail.
Misalignment and Lubrication Issues- Thermography can help see any poor lubrication of any components; this prevents any failure on the equipment meaning your day can keep moving smoothly.
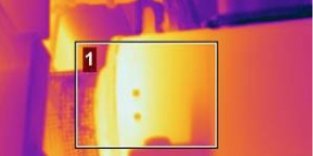
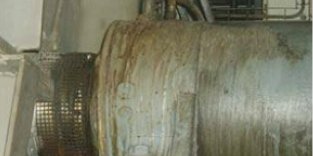
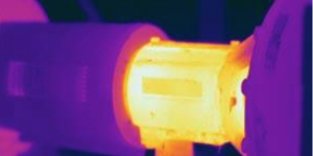
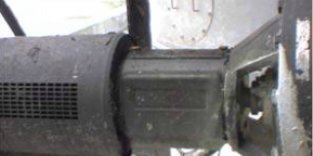
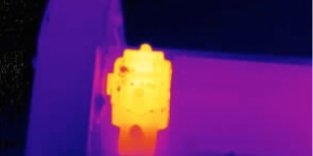
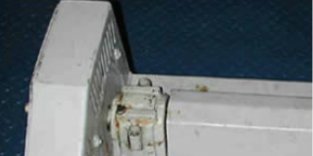
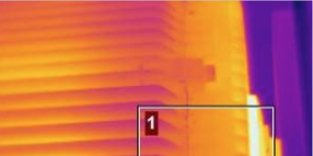
Questions About Mechanical Thermography Surveys Answered
-
Mechanical thermal imaging is a diagnostic technique that uses infrared cameras to detect heat patterns and temperature changes in mechanical systems. By identifying areas of abnormal heat, such as overheating components or friction in moving parts, it helps pinpoint potential problems before they escalate into costly failures.
-
Abnormal temperature changes often indicate underlying mechanical issues. Thermal imaging allows you to identify these problems early, preventing breakdowns that could disrupt operations. This approach not only helps you avoid costly repairs but also ensures your equipment runs efficiently, minimising downtime and maximising productivity.
-
Thermal imaging is highly effective in uncovering a wide range of issues. It can identify overheating bearings and motors, which may indicate excessive friction or wear. It can also reveal steam trap malfunctions, helping to improve energy efficiency, and pinpoint blockages or leaks in pipes or valves, reducing the risk of further damage. By addressing these problems early, you can save time and resources while protecting your equipment.
-
Unlike many traditional diagnostic approaches, thermal imaging is non-invasive and doesn’t require disassembling equipment or shutting down operations. This means you can identify issues without interrupting your workflow. It also provides immediate visual feedback, allowing for faster and more informed decision-making compared to slower or more intrusive methods.
-
A mechanical thermal imaging survey typically begins with a risk assessment and method statement tailored to your specific equipment and operational environment. Once the survey is conducted, you’ll receive a detailed report that includes both thermal and digital images of key components. This report provides clear insights into potential risks and offers actionable recommendations for preventative maintenance, helping you address issues before they escalate.
-
The frequency of thermal imaging surveys depends on your equipment’s operational demands. For high-strain systems, regular monitoring may be necessary to ensure continuous performance and avoid unexpected failures. For systems under less strain, occasional checks may suffice. Consulting with a professional can help you determine the best schedule based on your specific needs.
Contact Us For an Mechanical Thermal Survey
We're on hand to help with anything you require, so get in touch on 01234 219421 to discuss your project with us; alternatively, send us a message to support@thermascan.co.uk and we’ll answer all your questions.
Looking for your own surveying camera?